When it comes to creating custom labels, one of the most important choices you’ll make is the type of label adhesive to use.
Whether you need a label that sticks forever or one that comes off easily, the right adhesive is key. It makes sure your labels stay in place until you want to take them off.
In this guide, we will explain the different types of adhesives for custom labels. We will also show how laminates can add extra protection. Finally, we will give tips on choosing the right adhesive for your needs.
Permanent vs. Removable Label Adhesives
Key Characteristics of Permanent Adhesives
Permanent label adhesives are designed to create a strong, long-lasting bond with the surface they are applied to. Once you apply these labels, you find them difficult to remove without leaving behind residue or damaging the surface.
This makes permanent adhesives ideal for labels that need to stay in place for the long term, such as:
➡️ Product packaging
➡️ Equipment tags
➡️ Warning or instruction labels
Permanent adhesives are usually made to withstand various conditions, including heat, moisture, and exposure to chemicals. These qualities ensure that the label won’t peel or fall off, making them perfect for heavy-duty applications.
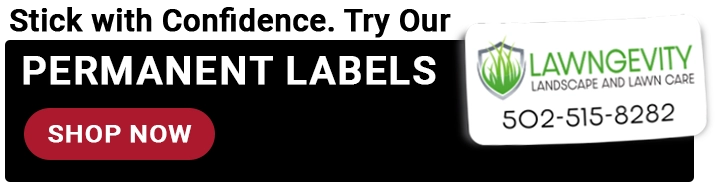
Applications for Removable Adhesives
On the flip side, removable label adhesives are designed to stick securely but allow for easy removal when needed. These labels peel off cleanly without leaving any sticky residue behind, making them ideal for temporary uses such as:
➡️ Promotional stickers
➡️ Price tags
➡️ Event or name badges
Removable adhesives are helpful when you need a label for a short time. They won’t damage the surface when you take them off.
However, keep in mind that while these adhesives are removable, they are still durable enough to stay attached until they are intentionally peeled off.
Adding Laminates for Extra Label Protection
Benefits of Laminates: Durability, UV Protection, and More
While the label adhesive determines how well the label sticks, a laminate provides an extra layer of protection.
Laminates are clear, thin films placed over your label. They protect it from damage caused by moisture, UV rays, or chemicals. This added protection makes the label last longer and prevents fading, scratches, or peeling.
Here’s how laminates can benefit your custom labels:
- Durability: Laminates protect your label from general wear and tear, ensuring the design and information stay legible over time.
- UV Protection: For labels used outdoors, laminates can shield against sunlight, preventing colors from fading.
- Moisture Resistance: If your labels will be exposed to water or humidity, laminates help them stay intact and avoid smudging.
Popular Laminates: Gloss, Matte, and Textured Finishes
When choosing a laminate, you can also select from different finishes to match the look you’re going for:
- Gloss Finish: This laminate gives your label a shiny, polished appearance and enhances colors, making them pop.
- Matte Finish: For a more subtle, non-glossy look, matte laminates are ideal. They reduce glare and give the label a smooth finish.
Textured Finish: Some laminates come with a textured surface, which adds a tactile element and gives the label a unique feel. This can be particularly appealing for premium products or decorative purposes.
How to Choose the Right Adhesive for Your Custom Label
Factors to Consider: Surface, Duration, and Environment
When selecting the right label adhesive, it’s important to consider where and how the label will be used. Here are some key factors to keep in mind:
- Surface: Different adhesives work better on certain surfaces. For example, smooth surfaces like glass or plastic need a different adhesive than rough materials like wood or fabric.
- Duration: How long does the label need to stay on the surface? If it’s a permanent label, a strong adhesive is crucial. If it’s a temporary sticker, go with a removable adhesive.
- Environment: Will you use the label indoors or outdoors? Will it face exposure to moisture, heat, or chemicals? These environmental factors can impact how well the adhesive holds up over time.
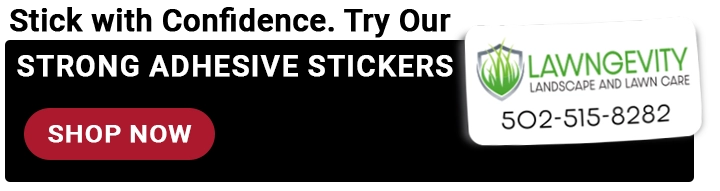
Testing Adhesives Before Full Production
It’s a good idea to test the label adhesive before starting full production. This is important if you’re unsure how it will work on your chosen surface.
Apply a few sample labels and monitor how well they stick under normal conditions. This testing phase can help you avoid issues like peeling, poor adhesion, or leftover residue after removal.
Testing also ensures that your labels will meet the durability and performance standards needed for their intended use.
Understanding the Different Adhesive Types FAQs
Yes, many types of label adhesives are available with varying strengths to suit different surfaces. For example, you might need a stronger adhesive for rough or uneven surfaces. A standard adhesive may work well on smooth surfaces like glass or plastic.
For outdoor labels, we recommend using permanent adhesives paired with UV-protective laminates. These adhesives can handle tough weather, like sunlight, rain, and extreme temperatures. This keeps your labels intact for a long time.
Laminates protect custom labels by adding a transparent layer over the label design. This layer shields the label from moisture, UV rays, and abrasion, which helps the label maintain its appearance and functionality for a longer period, especially in challenging environments.
Before You Go…
Choosing the right label adhesive is crucial to making sure your custom labels stay put and perform well, no matter where they’re applied.
Whether you need labels for temporary promotions, product packaging, or outdoor use, Maverick Label offers a range of adhesives and laminates to suit your specific needs. Visit us to find more options and ensure your labels are built to last.