A warehouse control system (WCS) acts like GPS for your inventory, directing equipment, tracking products in real time, and making sure nothing gets lost in the shuffle.
When integrated with durable asset tags and scanning tech, it keeps warehouses moving efficiently, even when systems are under pressure. Asset tags are the physical link that ensures this digital control delivers accurate, on-the-ground results.
What Is a Warehouse Control System (WCS)?
A warehouse control system is software that orchestrates warehouse floor operations in real time. It bridges the gap between high-level planning (done by WMS or ERP systems) and the execution that happens on conveyors, sorters, scanners, and storage units.
How It Differs from a Warehouse Management System (WMS)
While a WMS decides what needs to happen, the WCS decides how and when it gets done. Think of WMS as the planner and WCS as the air traffic controller ensuring every move happens safely, in sequence, and without collision.
Why Think of WCS as GPS for Your Warehouse
A GPS system helps people navigate roads. A WCS helps inventory navigate your warehouse with the same precision.
Visibility and Intelligent Routing
A WCS constantly monitors equipment and inventory movement. It knows when a package was scanned, where it’s headed, and how to reroute it if something fails, just like GPS suggesting a new route in traffic.
Reducing Errors and Lost Inventory
Without real-time corrections, misrouted items cause delays, lost stock, and unhappy customers. A WCS reduces manual intervention and uses rules to keep things running on target.
How a WCS Works: The Core Components
Understanding how a WCS operates reveals where the real gains come from, efficiency, accuracy, and control. These systems link physical processes with real-time digital decisions, turning warehouse equipment into a coordinated network.
Hardware Integration and Device Control
A WCS interfaces directly with warehouse machinery, sending commands to execute physical tasks quickly and correctly.
- Conveyors: Start, stop, or reroute packages based on item destination.
- Barcode scanners: Trigger item identification and location updates automatically.
- Pick-to-light systems: Illuminate correct bins for pickers, reducing errors.
- Sorters and diverters: Direct items down the correct path based on WCS rules.
Example: A WCS detects that a package meant for Zone B is heading toward Zone A. It halts the conveyor, reroutes the item, and updates the system, all in milliseconds, without operator input.
Communication with WMS and ERP Systems
The WCS sits below systems like WMS or ERP, translating big-picture plans into minute-by-minute commands.
- Receives order data: Item, quantity, storage location, and destination.
- Breaks down tasks: Assigns those items to picking, packing, sorting, and staging.
- Sends instructions to equipment: Triggers devices or prompts human actions.
Example: A WMS flags an order for 10 units of Item X. The WCS determines which storage zone it’s in, tells the operator or machine where to pick it, and coordinates delivery to the correct dock.
Logic Layer: Rules-Based Decision Making
This is where the WCS becomes intelligent, not just executing commands but making decisions based on conditions on the ground.
- Condition checks: Is the destination zone full? Has this item already been scanned?
- Rule application: Send fragile items on slower conveyors; route heavy items to reinforced zones.
- Real-time adjustments: If one line is down, automatically reroute without delay.
Example: A scanner flags an item too large for its assigned chute. The WCS overrides the default route and sends it to a manual handling zone, preventing a jam and a shutdown.
When Do You Need a Warehouse Control System?
Signs Your Warehouse Is Ready
- You’re operating or planning to add automation (sorters, conveyors, AS/RS)
- Operators are making too many manual decisions
- Shipments are delayed due to misrouted or misplaced items
- Your team spends time fixing errors rather than moving orders
Questions to Ask Before Implementing
- Do you already have a WMS, or is this your first step into digital logistics?
- What’s the volume of items you process per hour/day?
- Are current asset tags compatible with automation scanning?
Key Benefits of Implementing a WCS
Efficiency, Accuracy, and Cost Reduction
A WCS minimizes idle time and maximizes throughput. Fewer manual tasks mean faster processing and fewer human errors, translating to cost savings.
Operator Guidance and Workflow Optimization
WCS can direct operators step by step, reducing training time and improving output consistency. It keeps the floor in sync even during shift changes or high-volume windows.
Common Use Cases: Where WCS Delivers Value
High-Volume Distribution Centers
Large operations processing thousands of items per day benefit from WCS coordination—especially where speed and accuracy directly affect revenue.
Automated Material Handling Environments
If your warehouse uses any sort of automation, from pick modules to robotic arms, a WCS becomes the command center that makes sure each piece of equipment stays in sync.
Choosing the Right Asset Tags for WCS Accuracy
Why Durable, Scannable Labels Matter
Barcode or QR code misreads due to fading, tearing, or surface damage throw off the whole system. Reliable WCS performance starts with reliable physical identification.
Recommended Tags for Harsh or Fast-Moving Environments
- Metal barcode tags for heavy equipment and exposed surfaces
- Polyester labels for plastic bins and painted metals
- Tamper-evident labels for tools or electronics subject to movement or risk
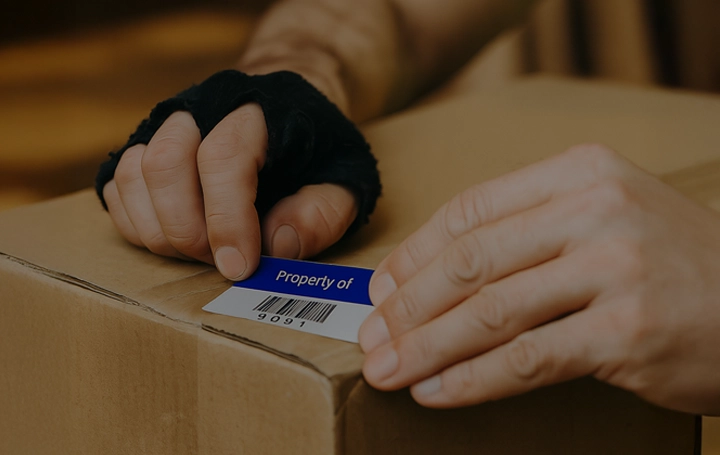
How to Integrate a WCS into Your Existing Workflow
Planning and Phased Implementation
Avoid a rip-and-replace approach. Start with a small zone, test flows, and gradually scale across the facility.
Training, Maintenance, and Tag Inspection
Train operators on equipment interaction and scanning workflows. Build periodic label inspection into scheduled maintenance to keep systems aligned.
Case Study: Mid-Sized Retailer Doubles Throughput with WCS
A retail distribution center handling 4,000 SKUs faced bottlenecks and misroutes during peak season. By implementing a WCS integrated with durable serialized tags and zone-based scanning, they doubled throughput and reduced manual errors by 60%—with no increase in staffing.
Smarter Tracking Begins with Better Visibility
If your warehouse runs on automation, or plans to, adding a warehouse control system is the next step toward operational clarity. It’s not just about moving boxes faster; it’s about moving them smarter. Start with accurate identification using high-durability asset tags built for WCS environments and build upward from there.
Warehouse Control System FAQs
It directs real-time activity on the warehouse floor, telling conveyors, scanners, and sorters how and when to move each item.
Not better—just different. WMS plans the workflow; WCS executes it by giving direct instructions to machines and operators.
Durable, scannable labels like polyester, metal, or tamper-evident asset tags ensure smooth operation and prevent misreads.
Not necessarily. Many systems can be integrated into existing infrastructure through phased implementation and software layering.
If you’re struggling with volume, misroutes, or scaling automation, WCS is likely the next logical step.
It can. By automating decision-making and reducing human errors, it allows smaller teams to manage higher volume with less friction.
Costs vary widely based on system complexity and scale, but phased integration and using existing infrastructure can reduce initial expenses.